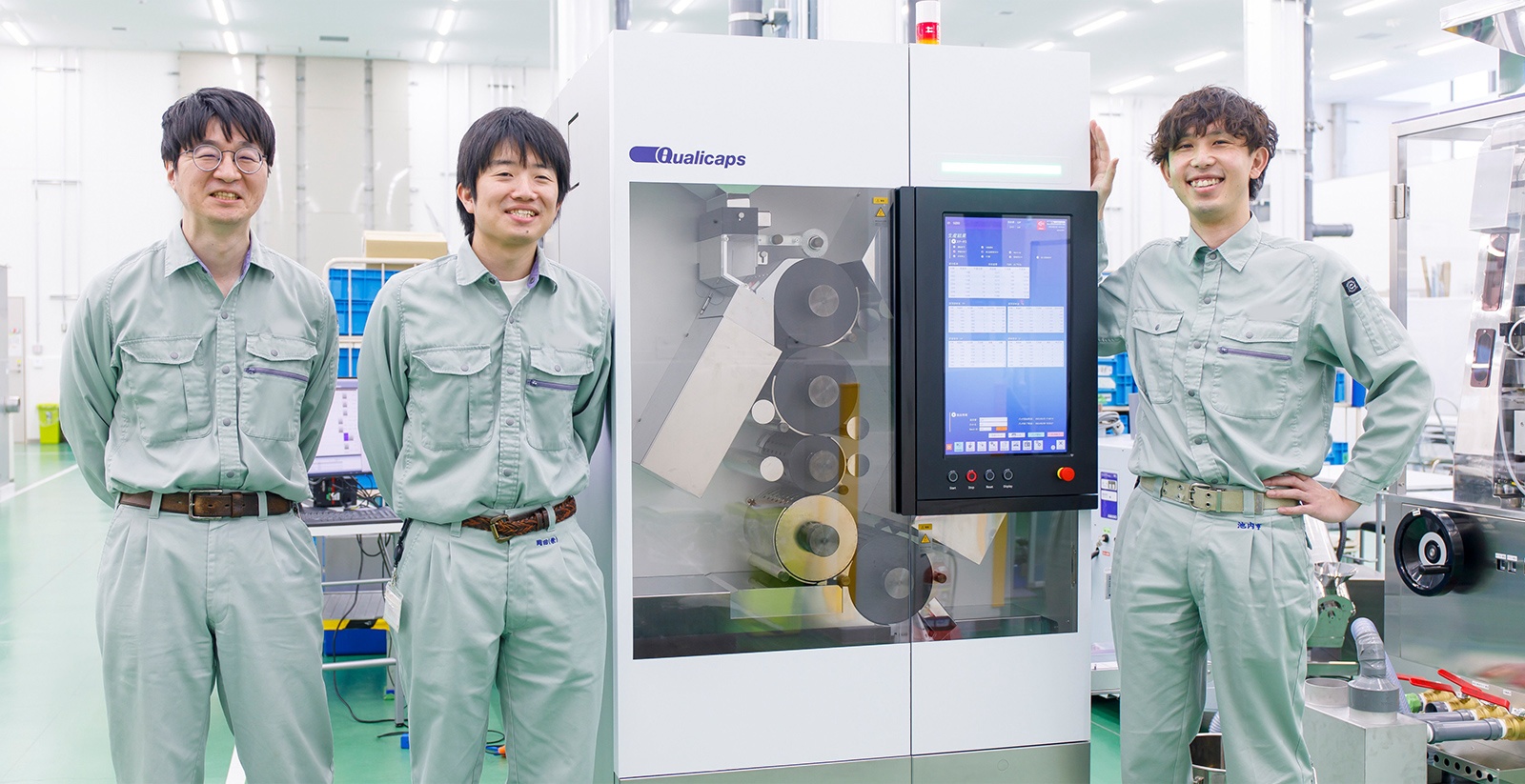
知られざる錠剤印字機械開発の奥深さ
Project
Story
プロジェクトストーリー
Qwv
ハードカプセルの外観検査・物質選別複合機
INTRODUCTION
クオリカプスの
コア技術と新発想で
世界最速&世界初に挑む
ハードカプセルへの薬剤充填後に必須である質量検査と外観検査。製薬メーカーにとっては、品質に大きく影響する製造プロセスにおいて、作業の無駄と様々なコストを省くことを目的に生み出されたのが、ハードカプセルの外観検査・質量選別複合機「Qwv」だ。この機械の特徴は、従来別々だった2つの装置を業界で初めて一体化した上に、質量検査は一カプセルあたり約0.2秒という世界最速のスペックを持っていること。省スペース化、省人化、機器導入コストやランニングコストも低減するなど、導入側にとっても多くのメリットをもたらすことができる。まさにオンリーワン&ナンバーワンと言うに相応しい製品誕生の背景にあった、技術者らの飽くなき挑戦の日々とは。
Project MEMBER
-
機械設計担当
K.I
プロジェクトリーダー
2012年入社
理工学部 機械工学科卒 -
光学設計・検査ソフトウェア担当
N.Y
2013年入社
電気工学専攻卒 -
電気設計・制御ソフトウェア担当
T.O
2010年入社
工学研究科 電気情報工学専攻卒
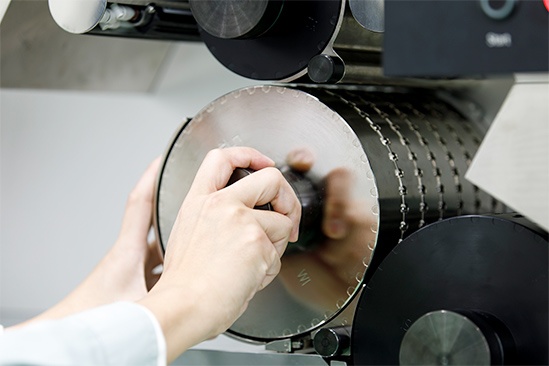
Project Story 01
1人の技術者の
アイデアから始まった
新たな挑戦。
2019年4月、クオリカプスは製剤機械の新規開発・技術研究に特化した組織として、各部の技術者を集めた開発部を新設。立上げ間もない頃、「このチャンスを絶対に逃してはならない」と新製品アイデアを温めていた1人の機械設計者が動いた。質量検査機と外観検査機を一つにまとめ、よりコンパクトで高性能な製品にしたいという企画を提出したのだ。部門長から「ポイントとなる質量計測スピードをどのように高めるのかの実験から始めてみてはどうか」という回答をもらい、夏頃からこの部分に絞り込んで実験をスタートさせた。
「はじめは失敗して元々という気持ちで、自由にやらせてもらっていました。上手くいかなかったら…という不安よりも、チャレンジするワクワク感の方が強かったと思います」
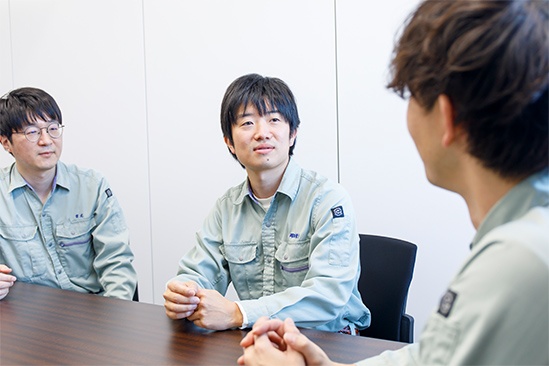
そう語るように、当初はひたすら挑戦できる環境を楽しみながら取り組んでいたという。ただ、誰もが予想できるように、いずれ「従来機と同等のスペックを持たせた中で、機能を一体化して省スペース化すること」を実現するには既存のものをそのまま活かすことはできず、あらゆる部分を一新しなければならなかった。新たな発想とトライアンドエラーがいくつも必要となり、想定外の動きやトラブルが出るたびに原因を分析し解決する、という地道な積み重ねをする他に術はなかったのである。
特にプロジェクトリーダーが最重要ミッションと考えたのは、「質量検査のスピードを外観検査と同等以上にする」ということ。1錠あたり約0.2秒という検査スピードを実現できなければ外観検査のスピードを落とす必要があり、複合機としてのスペックも下がってしまうと考えていたのだ。だが最初は、約0.4秒と目標値には遠く及ばない結果であった。
装置の構造を見直し、時間短縮の方法を探っていくのと並行して電気設計・制御ソフトウェア担当が、質量を計量する秤のノイズが想定以上に大きいということに気づく。そこで彼は、振動や電磁波、静電気などを除去する方法を外部セミナーで学び、知見を獲得。実験機の部品変更や配線へのカバー・フィルター装着といった改善を行った結果、検査スピードが向上し課題解決の目処をつけていった。 一方で、光学設計・検査ソフトウェア担当は、先行する2人の動きを見据えて外観検査機能で使用するパソコンの調整に着手。コンパクトな機械にできないかと準備を進めていた。
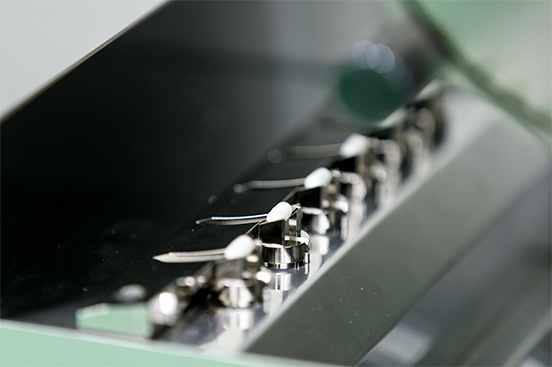
Project Story 02
開発部初の
大型プロジェクトに
持つ強い覚悟。
検査スピード向上の成果が見えてきた2020年初頭。本格的に開発へのGOサインが出され、発案者であるプロジェクトリーダーを筆頭に、電気設計・制御ソフトウェア担当、光学設計・検査ソフトウェア担当の3人で、開発部として初の大型プロジェクトは動き出した。
当初、3人の心にあったのは、「開発部の第一号案件だから、必ず成功させて部門のメンバーに良い影響を与えたい」という想い。それと同時に、社長や役員の前で「製造業の人員不足解決や働く人の環境改善のためにも、この製品をつくらせてほしい」と強く訴えた覚悟だった。
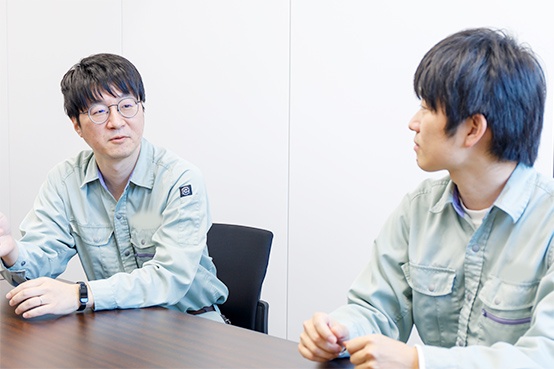
この「製造現場で働く人を考えたものづくり」を3人共通の開発軸としながら、さらなる質量検査スピードの高速化と安定化、カプセル搬送の仕組みの構築、外観検査の精度向上など、試行錯誤を繰り返す日々が始まった。 プロジェクトリーダーはまず、実験機では実現できた0.2秒という計測スピードを安定化させるため、部品の変更や改良に取り組んだ。電気設計・制御ソフトウェア担当は省スペース化に向けて、従来の半分サイズの制御盤をイチから製作し、さらに操作性を高めるためにタッチパネルの大型化やUIの改善にも注力。光学設計・検査ソフトウェア担当は外観検査の精度・スピード向上を目指して、カメラ以外の光学機器を一新するだけでなく、カプセル外観検査アプリケーションに対しても新たな機能追加に取り組んだ。
実験機の段階である程度の成果が出ていたため、順調にプロジェクトは進んだが、最後に発生したのが「従来機に比べ検査精度が低い」という問題。複合機にすることでノイズや振動が増えてしまったことが原因で、特に問題となっていたのが、カプセルを供給する機構の振動だった。
決定的な解決策は見つからず苦悩する日々が続いていた中、プロジェクトリーダーの発想の転換がブレイクスルーを生む。供給率を維持しつつ、振動を抑えた供給機構を生み出したのだ。これにより、プロジェクトが大きく前進したのだった。
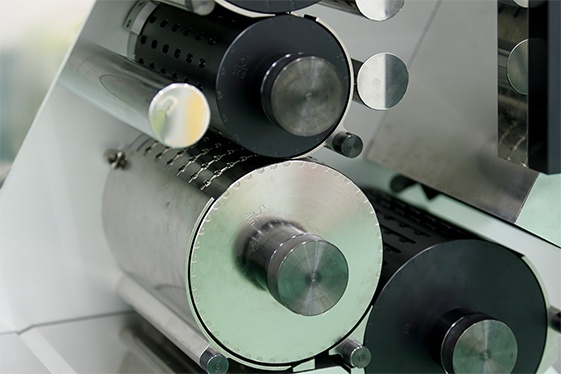
Project Story 03
「いくつもの特許技術を
生み出す」という
副次的な効果も。
その後、実験機の結果を踏まえて設計図を起こし、2021年の春に実機が完成。「Qwv」と名付けられ、今までのクオリカプスのプロダクトイメージを一新する外観デザインにもこだわった新型機が市場デビューを果たした。 世界最速クラスの「0.2秒の質量計測」を実現する仕組みと、独自のハードカプセル搬送の仕組み、さらに重さの不良品、外観の不良品、良品の3種を効率的に振り分ける機構など、「Qwv」開発時に生み出された数々の技術は、いくつも特許技術申請が成され、クオリカプスの技術力の高さを示す副次的な成果につながった。
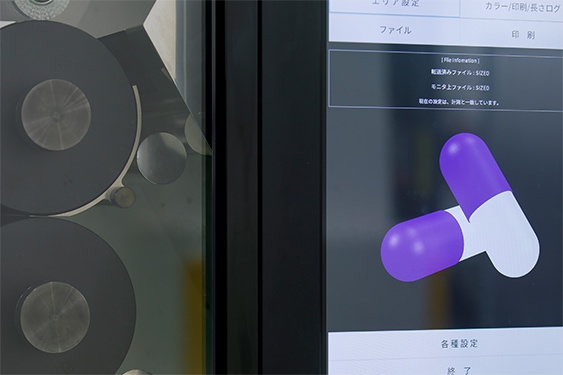
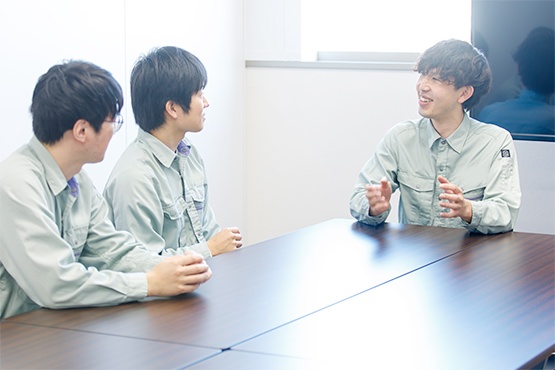
メンバーはこのプロジェクトを振り返り、「長年温めてきた装置のアイデアを自らの手で形にできたことは、本当にうれしいことでした。初めてイチから設計する経験ができましたし、クオリカプスのイメージを変えるプロダクトデザインへのチャレンジなど、あらゆる面で初挑戦できたことを技術者として幸せに思います。何より、自分たちで世界初の機械をつくることができたのは、今後の技術者人生にも大きな意味を持つと思います」
「課題解決のために新しい技術を勉強したことで、大きく成長できたなと実感しています。それだけでなく、限られた時間・予算の中で何を優先するか考えるようになったこと、新しい要素を取り入れながらバランスの良い製品開発を目指すようになったことは、働く上で新たな視点を得られたので、本当に良い経験だったと感じています」
「検査アプリケーションを大幅に改良し、新たなアルゴリズムや新機能の追加を行う中で試行錯誤を繰り返し、解決策を探る経験は、新発想や新たな知見を得る機会となり、今後の案件でも活かすことが出来そうです。クオリカプスの自由度の高い開発環境の良さを、改めて感じられる時間でした」
と語るように、3人にとっても大きな手応えと技術者としての成長をもたらした。
製品発表後すぐに1台目を受注し、以降も業界から注目される「Qwv」。その「世界最速の性能、他社にはない複合機」というオンリーワンの魅力は、クオリカプスのさらなる市場拡大を支えていくだろう。そして、ヘルスケア業界の人員不足解決や労働環境の改善といった、製造現場が持つ多くの課題解決に寄与していくことに違いない。