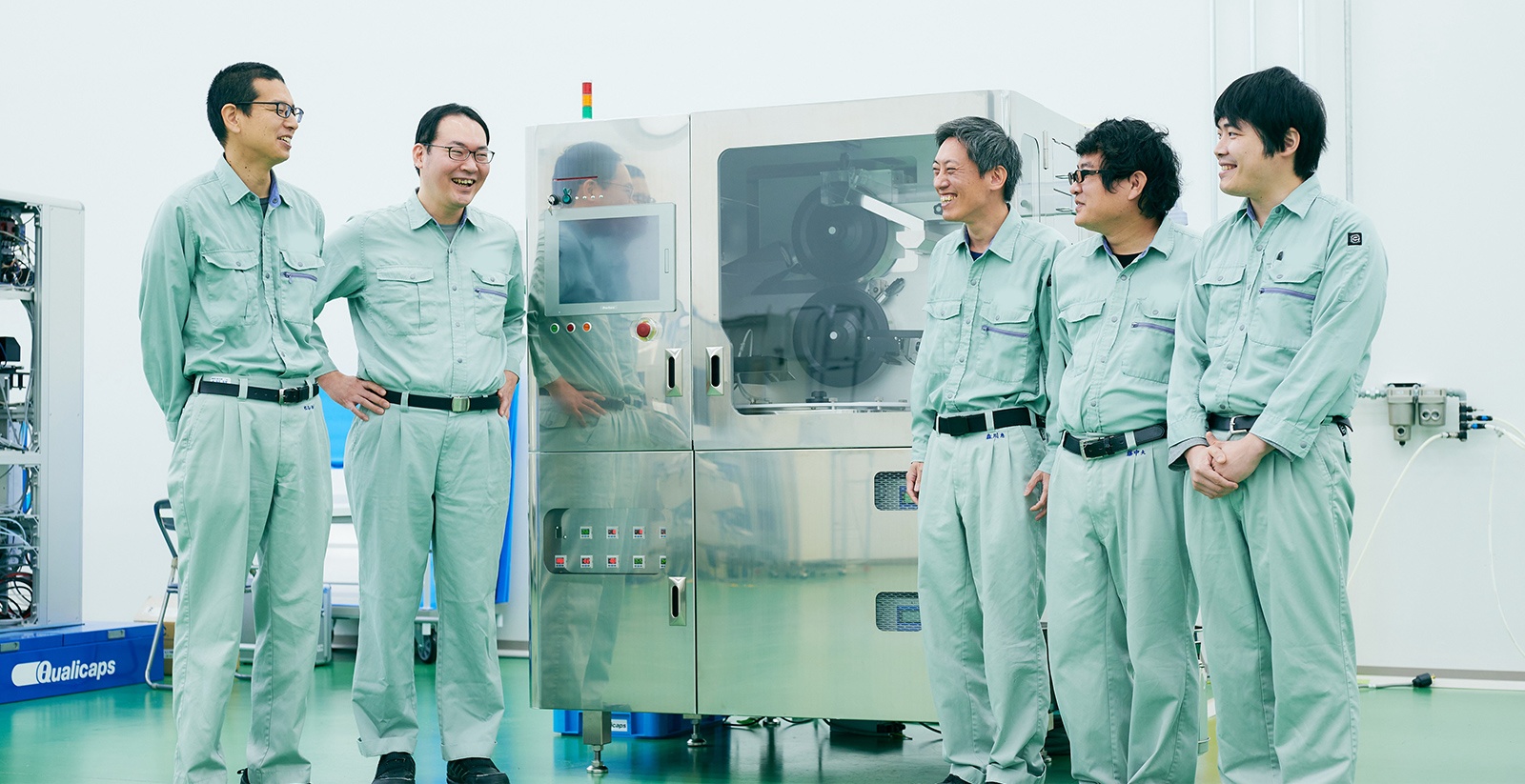
知られざる錠剤印字機械開発の奥深さ
Project
Story
プロジェクトストーリー
QUALIS
UVレーザマーキング装置
INTRODUCTION
世界をリードする
新製品を生み出せ。
クオリカプスはUVレーザマーキング装置「LIS-250D」によって「非接触式レーザ印刷」という新たな印字方法のジャンルを医薬品業界で確立し、その後、次世代のUVレーザマーキング装置「QUALIS」を2018年に完成させた。「QUALIS」の開発テーマは『世界市場をリードする超高速搬送UVレーザマーキング装置』であった。この超高速搬送UVレーザマーキング装置「QUALIS」はいかにして開発に至ったのか。最先端の技術をいち早く導入する挑戦心と、「自分たちの技術で世界の医療に貢献したい」という熱い思いを持った技術者らの物語から読み解いていく。
Project MEMBER
-
機械設計担当
プロジェクトリーダーK.M
2008年入社
工学部 機械工学科卒 -
部品設計担当
K.F
2012年入社
工学部 機械工学科卒 -
電気回路担当
M.M
2017年入社
電気工学科卒 -
電気設計担当
D.F
2018年入社
電気工学科卒 -
ソフトウェア担当
K.O
2018年入社
マルチメディア学科卒
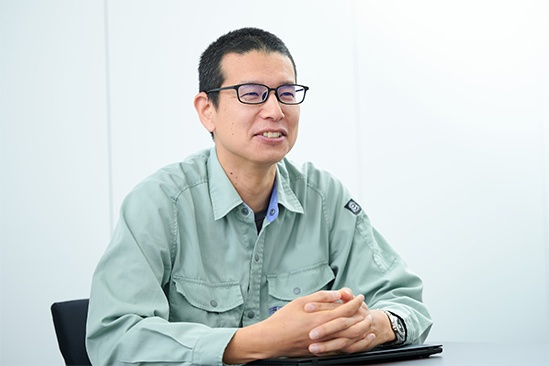
Project Story 01
UVレーザを用いた
革新的な印刷技術の
実用化。
「世界の製薬市場に向けて、どこにも負けないUVレーザマーキング装置を開発できないか?」。2016年当時、その話を海外営業の担当者から聞いたとき、マーキング装置の開発リーダーは「ならば世界最速に挑戦しよう」とすぐさま思いついた。
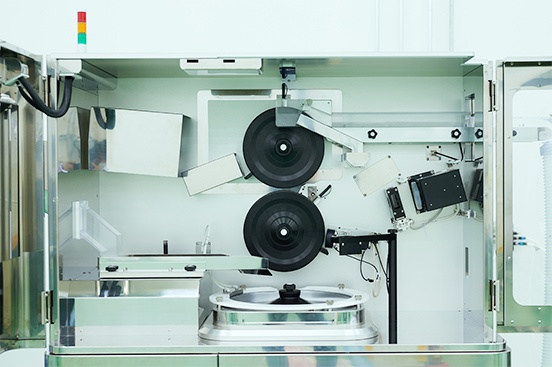
それまで、固形製剤への印刷ではインク方式が広く用いられてきたが、近年は印刷のコストや品質などの理由から“脱インク”のニーズが高まっている。その決め手となるのが、UVレーザだ。UVレーザによって、錠剤にコーティングされている酸化チタンの酸素原子を離脱させ、チタン原子と酸素原子の比率を変化させることにより、酸化チタンが白からグレーになる仕組みだ。レーザを照射しても薬の有効成分に影響を及ぼすことはなく、インク方式に比べて印刷も高精度。また、インクが不要となる分、印刷コストを抑えられる上、インクの飛び散りといった問題を解消できるなどメリットも多い。お客様である製薬メーカーはこのメリットに対する関心が高く、「ぜひ製品化に取り組んでほしい」と依頼が来たことから、クオリカプスでは、国産初のUVレーザマーキング装置「LIS-250D」を開発し、販売を開始した。医薬品業界での評価は高く、相次いで受注するヒット作となったのである。
そしてその後、UVレーザマーキング装置を海外市場に向けて本格的に販売していくため、「LIS-250D」に続いた新機種の開発に挑むこととなった。世界の製薬業界では、メガファーマといわれる世界規模の製薬会社が多数存在する。それだけに生産規模も大きく、マーキング装置としても「生産性がより高く、しかもコストメリットのある製品」が不可欠であった。開発リーダーが世界最速への挑戦を意識したのも、こうした事情を踏まえてのことである。そこでプロジェクトメンバーは、「LIS-250D」から開発方針を一新し、機構の異なるUVレーザマーキング装置をめざしたのである。
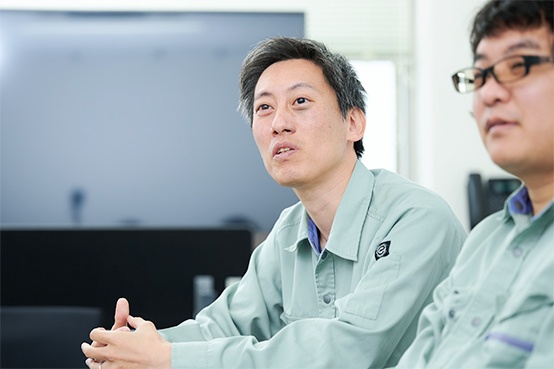
Project Story 02
超高速搬送へ
総力を挙げた
あくなき挑戦。
「ひとくちに固形製剤といっても、大きさや形状はさまざま。それぞれに的確に対応して印刷するには、装置の事前調整が欠かせません。しかし、調整をもっと省力化できないかというご要望をいただき、この課題の解決を重視しました」(開発リーダー) 「LIS-250D」では、固形製剤を1ラインに12個ある型に送り込んで印刷していく。同じ固形製剤を大量に印刷する時には大きなメリットがある反面、異なるものを印刷しようとすると、その都度、型を交換して調整する必要がある。各々の型の費用および調整に時間を要したのである。そこで新機種では、型の交換をなくすという大胆な設計を模索した。
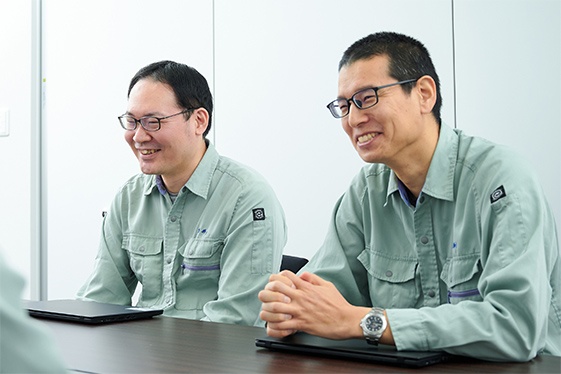
開発した機構は、固形製剤を1列に並べて順々に印刷するというもの。単純に考えると、1ライン12個並べる印刷に比べてかなり遅くなると思える。しかし、クオリカプスの超高速で搬送する技術を用いた結果、「LIS-250D」の毎時25万錠に対して、新機種「QUALIS」は40万錠の印刷を可能にした。
超高速搬送を可能にしたことについては、機構の見直しに加えて制御プログラムの刷新が見逃せない。従来用いられてきたPLCと呼ばれる制御装置は、信頼性がきわめて高いものの、リアルタイムでは処理時間の短縮に限界がある。今回のような超高速搬送には対応できなかった。そこでソフトウェアエンジニアが提案したのが、世界で主流となりつつあるPCによるリアルタイム制御。若手エンジニアが中心となって開発を担当し、中堅エンジニアも機械と制御の橋渡しをしっかりと支えた。
「大きさや形の異なるものすべてに対応できる印刷方法というと、つまりは型をなくしてしまえということなのですが、実行するのはそう簡単ではありません。ただ、当社には製剤機械開発で培った『小さな物体を高速で搬送する要素技術』がありました。それを活かして新たな機構を設計し、真空吸着装置で固形製剤を吸い上げて搬送・印刷するというシンプルな方式を採用したのです」
「一般的にエンジニアの固定概念として、『PLCじゃないと制御系の開発は無理』というのがあります。しかし今回、若手ががんばったおかげで『できるはずがない』の壁を見事にぶち破りました。失敗を恐れることなく挑む社風と、上に立つ者が挑戦する姿勢を見せるからこそ、若い世代も積極的にチャレンジしてくれたのだと思います」
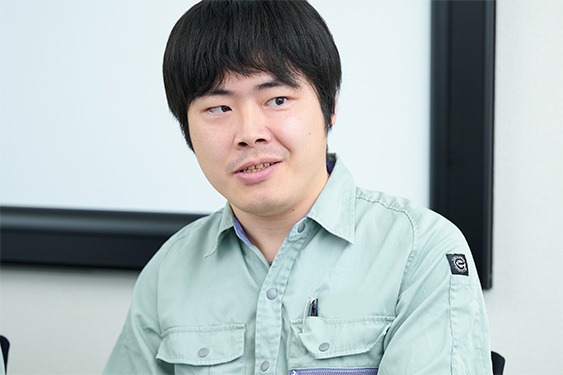
Project Story 03
「世界一をめざせ」
の思いが
ブレイクスルーを
可能に。
超高速搬送をクリアするためのもう一つ大きな課題が、機構の挙動をいかに検証するかであった。流れがあまりにも速すぎるため、肉眼ではもちろん把握できない。固形製剤の印刷ずれが生じた時も、メンバーはその現象を解明するのに苦労した。
超高速搬送という大きなポイントのほかに、世界一をめざすうえでは装置のコンパクト化も必須であった。しかし、装置全体を小さくすることは、組み立てが難しくなるだけでなく、メンテナンスがしにくくなるという問題も生じかねない。特に難しかったのは、冷却用の水を通す経路の設計。万が一、稼働中に水漏れが生じると大問題につながるということも意識しながら、部品点数を減らし全体のコンパクト化を進めていった。さらにメンテナンス面でも、錠剤の排出位置を高くしたことで、外観検査をはじめとする後工程の設備設計を容易なものにするなど、コンパクト化と同時に導入後の使いやすさも徹底的に意識した。
また、コンパクト化の過程では、若手エンジニアの提案で丸みを帯びた筐体が採用された。産業機械といえども、海外市場ではデザインも重視されるからだ。操作パネルの画面デザインも若手が工夫を凝らして先進的なものとした。
「問題がはたしてリレーなのか、センサーなのか、ソフトウェアなのか。メンバー総出で解明に当たりました。オシロスコープの波形を延々と見つめたり、カメラのスローモードで挙動を何百枚と撮影したり……。いずれも根気のいる仕事でしたが、メンバー全員が『世界一をめざせ』の思いを持っていたので、粘り強く取り組めました」
「装置はだれもが直感的に操作できることが理想。だから、見た目も重要です。この期間はデザイン関係の本を読みあさったり、街角のサイネージをじっくり眺めたりと四六時中、デザインのことばかり考えていました。最終的には、文字による表示はなるべく控えて、アイコンやグラフを多用したインターフェースにしています」
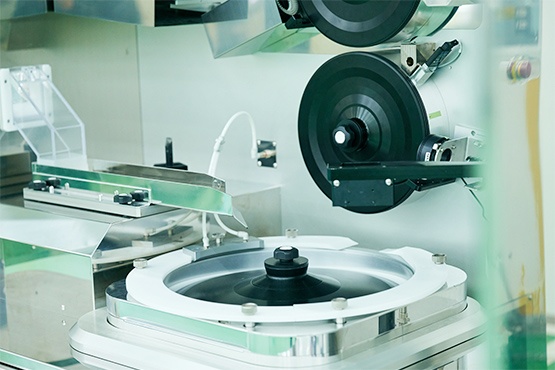
Project Story 04
困難を乗り越えた
からこそ得た
自信と挑戦心。
PCによる制御に限らず、他の分野で新たな手法を次々取り入れた点も、今回のプロジェクトでは注目だ。それらを担ったのも主に若手のエンジニアたち。たとえば、機械設計では3D-CADを全面的に取り入れている。
また、電気回路図の設計にも専用のCADを導入。これらによって、設計の正確さとスピードアップの両立を実現した。
そして2018年、「LIS-250D」に続く新たなUVレーザマーキング装置がついに誕生した。製品名は社名の一部を冠した「QUALIS(クオリス)」と命名。今後、海外市場で展開していく上での、いわばフラッグシップとなる製品にしたいという思いが込められている。シンプルな搬送機構の採用により、1時間あたり最大40万錠もの印刷が可能な上、コンパクト設計により設置面積の省スペース化も実現した。お客様の反応は良好で、海外の展示会では引き合いが相次ぎ、デモ機が完成してからはすぐに一台売れた。その後、片面印刷から両面印刷もできるようになるなど、「QUALIS」はさらに改良が続いている。
マーキング装置の分野において、海外市場の開拓に向けて大きく前進するクオリカプス。事業が拡大していくとともに、エンジニアが活躍できるステージがますます広がっている。
「それまでもテスト的に運用はしていましたが、今回の設計では開発期間が限られていて、部品の試作を短期間で行う必要があったので、最初から3D-CADを用いました。今では新たなプロジェクトが立ち上がる時は、3D-CADを用いるということが増えてきています」
「実際に超高速で印刷される様子を見て、一つのプロジェクトをやり遂げるってこういうことなのだと胸が熱くなりました。開発過程では次々と問題が生じて、この先どうなるかと不安になったこともありますが、メンバー全員が力を合わせることで、どんな困難も乗り越えられると自信がつきました。これから先、世界一の製剤機械メーカーをめざして、さらに大きなプロジェクトに挑戦していきたいです」
「今のところ、UVレーザによるマーキングは、酸化チタンをコーティングした固形製剤にしか印刷できません。今後はどんな物に対しても、より正確かつ高速で印刷できる要素技術を開発し、製品化することに挑戦していきたい。当社にしかできないオンリーワンを世の中に出していきたいです」
「このプロジェクトでは、若手から中堅、ベテランの全員が持てる力を結集して成功をつかみました。お互いにさまざまなアイデアを出し合い、議論を重ねる中でよりよい製品へと進化していったと思います。自らのアイデアを具体的な形にしていく。そして、社会の役に立つ製品を生み出す。これこそエンジニアという仕事の醍醐味だと思います」